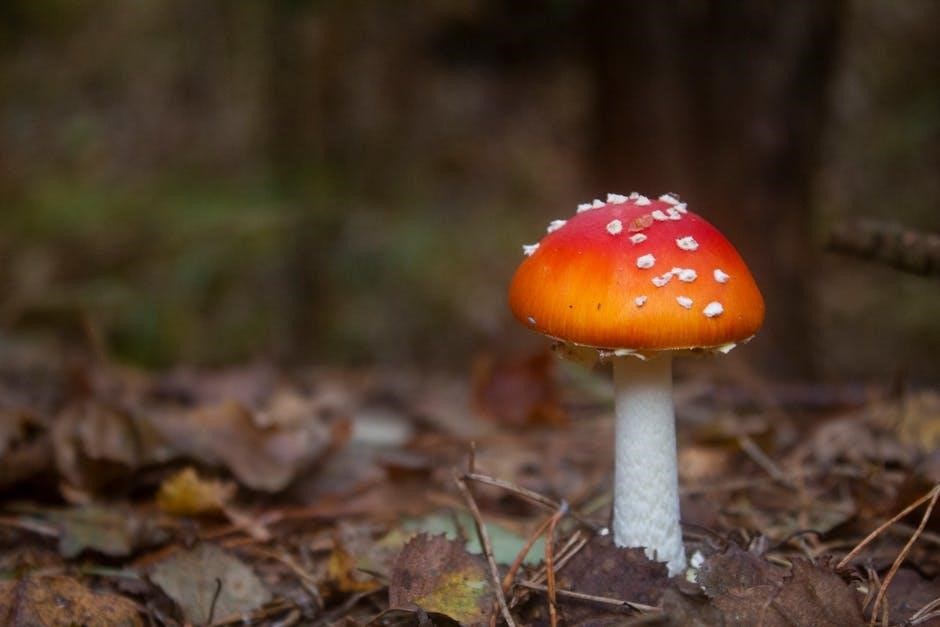
Soil stack systems in the UK are crucial for managing wastewater, ensuring compliance with regulations to maintain hygiene, ventilation, and environmental protection in residential and commercial buildings effectively.
1.1 Overview of Soil Stack Systems
A soil stack system is a critical component of a building’s drainage infrastructure, designed to safely transport wastewater and sewage from upper floors to underground drainage systems. These systems typically consist of vertical pipes, traps, and ventilation points, ensuring proper waste disposal while preventing sewer gases from entering the building. The stack pipes are usually installed along the exterior or interior walls, connecting sanitary fixtures like toilets, sinks, and showers to the main sewerage network. Effective ventilation is essential to maintain airflow, preventing siphonage of water traps and ensuring the system operates efficiently. Compliance with UK Building Regulations and British Standards, such as BS EN 12056-2, is mandatory to guarantee the system’s reliability, safety, and environmental protection. Proper design, installation, and maintenance of soil stack systems are vital to avoid blockages, odours, and structural issues.
1.2 Importance of Compliance with Regulations
Compliance with soil stack regulations in the UK is essential to ensure public health, safety, and environmental protection. Properly designed and installed systems prevent the spread of diseases by safely managing wastewater and sewage. Non-compliance can lead to structural damage, unpleasant odours, and contamination of water sources, posing serious health risks. Regulatory adherence also avoids legal penalties and ensures buildings meet minimum safety standards. Compliance guarantees the system’s efficiency, longevity, and reliability, reducing the likelihood of costly repairs. By following approved guidelines, such as those in Approved Document H, property owners can maintain hygiene, prevent pest infestations, and uphold property values. Ultimately, compliance ensures the system functions as intended, safeguarding both occupants and the environment from potential hazards.
Key Components of a Soil Stack System
A soil stack system includes stack pipes, air admittance valves, traps, and access points, essential for efficient drainage, ventilation, and hygiene in buildings, carrying waste, allowing airflow, preventing gases, and enabling maintenance.
2.1 Stack Pipes and Their Functions
Stack pipes are vertical pipes in a soil stack system, carrying wastewater from upper floors to underground drainage. Typically made of PVC or cast iron, they ensure efficient drainage and prevent sewer gases from entering buildings. Proper sizing, such as 50mm for systems without toilets, is crucial for handling wastewater flow effectively. These pipes connect sanitary fixtures to the main drainage system, maintaining hygiene and preventing odours. Their vertical design allows gravity to facilitate wastewater flow, while traps at connections prevent gas backflow. Stack pipes must comply with UK building regulations, ensuring durability and performance. Regular maintenance is essential to avoid blockages and corrosion, guaranteeing long-term functionality and compliance with safety standards. Proper installation and material selection are vital for reliability and adherence to regulatory requirements in both residential and commercial settings.
2.2 Air Admittance Valves and Their Role
Air admittance valves (AAVs) are essential components in soil stack systems, allowing air to enter the drainage system while preventing sewer gases from escaping. They are typically installed at the termination of soil stacks or vent pipes, ensuring proper ventilation without the need for external venting. AAVs maintain the balance of air pressure in the system, preventing siphonage of water traps and ensuring efficient drainage flow. They are particularly useful in multi-story buildings where venting through the roof is not feasible. Compliance with UK building regulations, such as Approved Document H, requires AAVs to meet specific standards for performance and installation. Properly fitted AAVs reduce odour issues and maintain hygiene, making them a critical part of modern drainage systems. Regular inspection and maintenance are recommended to ensure their functionality and system efficiency.
2.3 Traps and Their Significance
Traps are critical components in soil stack systems, serving as water seals that prevent sewer gases from entering buildings. Located under sanitary fixtures like sinks and toilets, traps create a barrier between the drainage system and indoor spaces. Their water-filled design ensures that harmful gases are trapped, maintaining indoor air quality and hygiene. Proper trap installation and maintenance are essential for preventing odours and ensuring the system’s efficiency. UK regulations, such as those outlined in Approved Document H, specify requirements for trap design, depth, and placement to ensure compliance. Regular inspections and cleaning are necessary to prevent blockages and maintain their functionality. Traps play a vital role in safeguarding public health and ensuring the smooth operation of drainage systems, making them a fundamental aspect of soil stack regulations in the UK. Their correct installation and upkeep are non-negotiable for system integrity and safety.
2.4 Access Points and Ventilation
Access points are essential for maintaining and inspecting soil stack systems, ensuring compliance with UK regulations. These points allow for the clearance of blockages and the inspection of system components, promoting efficiency and preventing potential issues. Properly installed access points must be strategically located to facilitate easy maintenance without compromising the system’s integrity. Ventilation is equally critical, as it maintains air pressure balance within the drainage system, preventing siphonage of water traps and sewer gas ingress. According to UK Building Regulations, ventilation pipes must terminate externally, often above roof level, to ensure effective airflow and odour dispersal. Materials such as uPVC or cast iron are commonly used for access points and ventilation components, adhering to durability and safety standards. Regular maintenance of these elements is vital to uphold system performance and compliance with regulatory requirements. Proper installation and ongoing care ensure the long-term functionality of soil stack systems.
UK Building Regulations for Soil Stacks
UK Building Regulations mandate soil stack compliance, ensuring safe and hygienic drainage systems. Approved Document H and BS EN 12056-2 provide detailed standards for materials, design, and installation;
3.1 Approved Document H: Drainage and Waste Disposal
Approved Document H of the UK Building Regulations provides detailed guidance on designing and installing soil stack systems. It ensures effective drainage, waste disposal, and ventilation, while preventing foul odours. The document outlines requirements for stack diameters, materials, and installation practices to maintain hygiene and efficiency. For instance, stacks serving toilets must have a minimum diameter of 110mm, while smaller systems may use 50mm pipes. Ventilation is critical, with termination points required to extend above roof level to prevent sewer gases from entering buildings. Compliance with these standards ensures safe and sustainable drainage systems, protecting both occupants and the environment. Proper adherence to Document H is essential for meeting legal and safety standards in the UK.
3.2 Materials and Workmanship Requirements
Materials used for soil stack systems must meet specific standards to ensure durability and performance. Approved materials include uPVC, cast iron, and HDPE, which are resistant to corrosion and suitable for wastewater drainage. Workmanship must comply with Building Regulations, with proper joints and connections to prevent leaks and ensure system integrity. Pipes should be installed with adequate support to avoid sagging, and all fittings must be compatible with the system. Regular inspections are required to verify that installations meet regulatory standards. Approved Document H and BS EN 12056-2 provide detailed guidance on acceptable materials and installation practices, ensuring compliance and long-term functionality of the drainage system.
3.4 Compliance with BS EN 12056-2 Standards
BS EN 12056-2 sets specific standards for gravity drainage systems inside buildings, including soil stacks. Compliance ensures systems are designed and installed to handle wastewater effectively. The standard outlines requirements for pipe sizing, gradients, and ventilation to prevent blockages and sewer gas issues. Air pressure testing is mandated to verify system integrity, using equipment like air bags, hoses, and gauges. Tests measure pressure drop over three minutes, ensuring minimal leakage. Traps must retain water to maintain positive pressure during testing. The standard applies to single stacks and multi-floor systems, providing clear guidelines for setup and evaluation. Adhering to BS EN 12056-2 guarantees reliable drainage performance, compliance with UK regulations, and protection against system failures. Proper testing and design ensure long-term functionality and safety in drainage systems.
Installation Guidelines for Soil Stacks
Soil stacks must be installed in accordance with UK regulations, ensuring proper location, securing, and accessibility. Materials and workmanship must comply with Approved Document H standards.
4.1 Location and Placement of Soil Stacks
Soil stacks should be located externally or internally, depending on the building design, ensuring accessibility for maintenance. External stacks must be positioned to avoid damage from weather or structural movements. Internal stacks should be placed in areas that allow easy access, such as stairwells or utility rooms, while minimizing disruption to living spaces. The placement must also consider the building’s structural integrity, avoiding areas prone to damage or settlement. Proper positioning ensures efficient drainage and ventilation, preventing blockages and odour issues. It is crucial to comply with UK Building Regulations and relevant standards for correct installation.
4.2 Diameter and Sizing of Discharge Stacks
The diameter of discharge stacks is critical to ensure efficient drainage and prevent blockages. The size is determined by the maximum flow rate and the number of fixtures served. For example, a 50mm diameter stack is suitable for systems not serving toilets, handling up to 1.2 litres per second. Larger diameters, such as 110mm, are required for stacks connected to toilets to accommodate higher flow rates. Proper sizing ensures optimal performance and compliance with UK Building Regulations, particularly Approved Document H. Incorrect sizing can lead to poor drainage, odour issues, and system failures. It is essential to consult relevant standards and calculations to determine the appropriate diameter for specific applications.
4.3 Connections to Underground Drainage Systems
Proper connections between soil stacks and underground drainage systems are essential for effective waste disposal and compliance with UK regulations. The connection must be made using approved fittings and ensure a watertight seal to prevent leaks and contamination. Direct connections to surface water drains are prohibited to avoid environmental pollution. The soil stack should connect to the underground drainage system via a trapped gully or similar approved fixture to prevent sewer gases from entering the building. Access points and traps must be installed to facilitate maintenance and inspection. The connection should also incorporate ventilation provisions to maintain air pressure balance and prevent siphonage of water seals in traps. Compliance with UK Building Regulations and BS EN standards ensures the system functions safely and efficiently. Proper installation is critical to avoid blockages and odour issues.
4.4 Use of Lintels and Bearings
Lintels and bearings are critical components in soil stack installations to ensure structural integrity and proper alignment. Lintels are used to support the soil stack where it passes through walls or floors, distributing the weight evenly and preventing collapse. Bearings must be installed at points where the stack rests on structural elements to allow smooth movement and reduce friction. Materials for lintels and bearings must comply with UK Building Regulations, typically requiring durable, corrosion-resistant materials such as steel or reinforced concrete. The sizing and positioning of these components are determined by the load they will carry and the stack’s diameter; Proper installation ensures the system remains stable and functional over time. Regular inspections are recommended to check for signs of wear or damage, ensuring long-term compliance with safety and performance standards. This maintains the structural and operational integrity of the soil stack system.
4.5 Termination Points and Ventilation Requirements
Termination points of soil stacks must be correctly positioned to ensure proper ventilation and prevent sewer gases from entering buildings; The termination point should be above the roof level, at least 900mm above any adjacent window or opening, to avoid odour issues. Ventilation is crucial to maintain air pressure balance in the system, preventing siphonage of water traps. Air admittance valves can be used as alternatives to traditional vent pipes, but they must comply with BS EN 12056-2 standards. The system must be designed to ensure airtightness, with all connections and seals meeting regulatory requirements. Proper termination and ventilation ensure the system functions efficiently, maintains hygiene, and prevents environmental contamination. Compliance with these requirements is essential for passing inspections and maintaining long-term system performance.
Testing and Inspection of Soil Stacks
Testing involves air pressure procedures to ensure system integrity, while inspections verify compliance with regulations, focusing on pipe condition, connections, and vent functionality to maintain hygiene standards effectively.
5.1 Air Pressure Testing Procedures
Air pressure testing is a critical step in verifying the integrity of soil stack systems. According to BS EN 12056-2, the test involves sealing the system and applying controlled air pressure. Equipment such as air bags, hoses, and pressure gauges are essential for accurate measurements. For single-stack systems, the test setup is straightforward, while multi-stack configurations require additional precautions to isolate each stack. Traps must be filled with water to create a positive pressure environment. The pressure drop over a three-minute period is monitored, and results must not exceed specified limits to ensure system tightness. This procedure ensures compliance with UK building regulations and guarantees the effective operation of drainage and ventilation systems. Proper testing helps identify leaks or weaknesses, ensuring long-term reliability and safety.
5.2 Inspection Requirements for Compliance
Inspections are essential to ensure soil stack systems meet UK building regulations and standards. Visual checks must verify that all components, including pipes, traps, and air admittance valves, are correctly installed and undamaged. Inspectors should ensure that pipe materials comply with Approved Document H and BS EN 12056-2 standards. Functional tests, such as water trap seals and ventilation flow, must be conducted to confirm system performance. Access points should be inspected for proper sealing and ease of maintenance. Documentation of inspections is required, detailing findings and any necessary repairs. Regular inspections by certified professionals help prevent issues and ensure ongoing compliance with safety and hygiene standards. Failure to meet inspection requirements can result in system failures or non-compliance penalties, emphasizing the importance of thorough and consistent evaluations.
Maintenance and Repair of Soil Stacks
Regular maintenance is crucial to prevent blockages, corrosion, and odours in soil stacks. Cleaning, inspections, and prompt repairs ensure system efficiency and compliance with UK regulations.
6.1 Cleaning and Clearing Blockages
Cleaning and clearing blockages in soil stacks are essential to maintain proper drainage and ventilation. Regular inspections should be conducted to identify potential issues early. Blockages often occur due to debris, grease, or foreign objects accumulating in the pipes. Professionals typically use tools like drain rods, high-pressure jetting equipment, or CCTV surveys to locate and remove obstructions. Property owners should also implement preventive measures, such as installing mesh screens over pipe openings to catch debris and scheduling periodic maintenance. Failure to address blockages can lead to backups, odours, and system damage. Compliance with UK regulations ensures that cleaning processes are environmentally safe and effective, preserving the integrity of the soil stack system and the overall drainage network.
6.2 Regular Inspections and Checks
Regular inspections and checks are vital to ensure the soil stack system operates efficiently and complies with UK regulations. Property owners should schedule periodic visual examinations to identify potential issues such as corrosion, blockages, or damage. Inspections should focus on key components, including traps, ventilation points, and pipe connections. Using specialized tools like CCTV cameras can help detect hidden problems within the pipework. Professionals should conduct these checks to ensure compliance with Approved Document H and other relevant standards. Regular maintenance not only prevents system failures but also ensures the overall hygiene and safety of the building. By addressing minor issues early, costly repairs can be avoided, and the longevity of the soil stack system can be maintained; Consistent inspections are a cornerstone of effective soil stack management in the UK.
6.3 Repairing Damaged or Corroded Pipes
Repairing damaged or corroded pipes in a soil stack system is essential to maintain functionality and prevent further deterioration. When damage is detected, professionals should assess the extent of the issue to determine the appropriate repair method. For minor corrosion or cracks, epoxy resin lining or patching may suffice. In cases of significant damage, replacing the affected pipe sections with compliant materials is necessary. Approved Document H and BS EN 12056-2 standards must be followed to ensure repairs meet regulatory requirements. Using durable, approved materials, such as PVC or ABS, ensures longevity. Proper sealing and testing post-repair are critical to prevent future issues. Regular inspections can help identify potential problems early, minimizing the need for extensive repairs. Timely and compliant repairs safeguard the system’s integrity and maintain hygiene standards in the building.
Common Issues and Solutions
Common issues with soil stacks include blockages, odours, and vent pipe problems. Solutions involve regular cleaning, using air admittance valves, and ensuring proper ventilation and material compliance.
7.1 Blockages and Their Prevention
Blockages in soil stacks are a common issue, often caused by debris, grease buildup, or improper waste disposal. To prevent blockages, regular maintenance is essential, including cleaning and inspections. Using enzymatic drain cleaners or high-pressure jetting can help clear clogs. Proper installation of traps and air admittance valves ensures efficient flow and ventilation, reducing the risk of blockages. Additionally, educating occupants on appropriate waste disposal practices, such as avoiding flushing non-biodegradable items, can significantly prevent blockages. Regular checks and adherence to UK Building Regulations, specifically Approved Document H, further ensure system functionality and longevity, maintaining hygiene and preventing costly repairs.
7.2 Odour Problems and Solutions
Odour issues in soil stack systems often arise from sewer gases entering buildings due to improper ventilation or blockages. These gases can cause unpleasant smells and health concerns. To address this, ensuring proper ventilation through air admittance valves or vent pipes is crucial. Regular inspections and cleaning of the system can prevent debris buildup, which contributes to odours. Traps under fixtures must remain filled with water to act as a barrier against sewer gases. Additionally, installing odour-sealing valves or using chemical treatments can help mitigate smells. Proper installation and maintenance, as per UK Building Regulations, are essential to prevent odour issues, ensuring a hygienic and safe environment. Addressing these problems promptly maintains system efficiency and occupant comfort.
7.3 Vent Pipe Issues and Remedies
Vent pipe issues are common in soil stack systems, often caused by blockages, incorrect termination, or lack of maintenance. Blockages can occur due to debris or nesting animals, disrupting ventilation and leading to drainage problems. Remedies include clearing blockages using professional equipment and ensuring proper installation. Vent pipes must terminate correctly, avoiding nearby windows or openings to prevent odour ingress. Regular inspections and cleaning are essential to maintain functionality. Additionally, installing air admittance valves can help regulate air pressure and reduce the need for external vents. Proper installation and adherence to UK Building Regulations ensure vent pipes function effectively, preventing issues and maintaining system efficiency. Addressing these problems promptly helps avoid costly repairs and ensures a hygienic environment. Regular maintenance is key to sustaining vent pipe performance and overall system health.